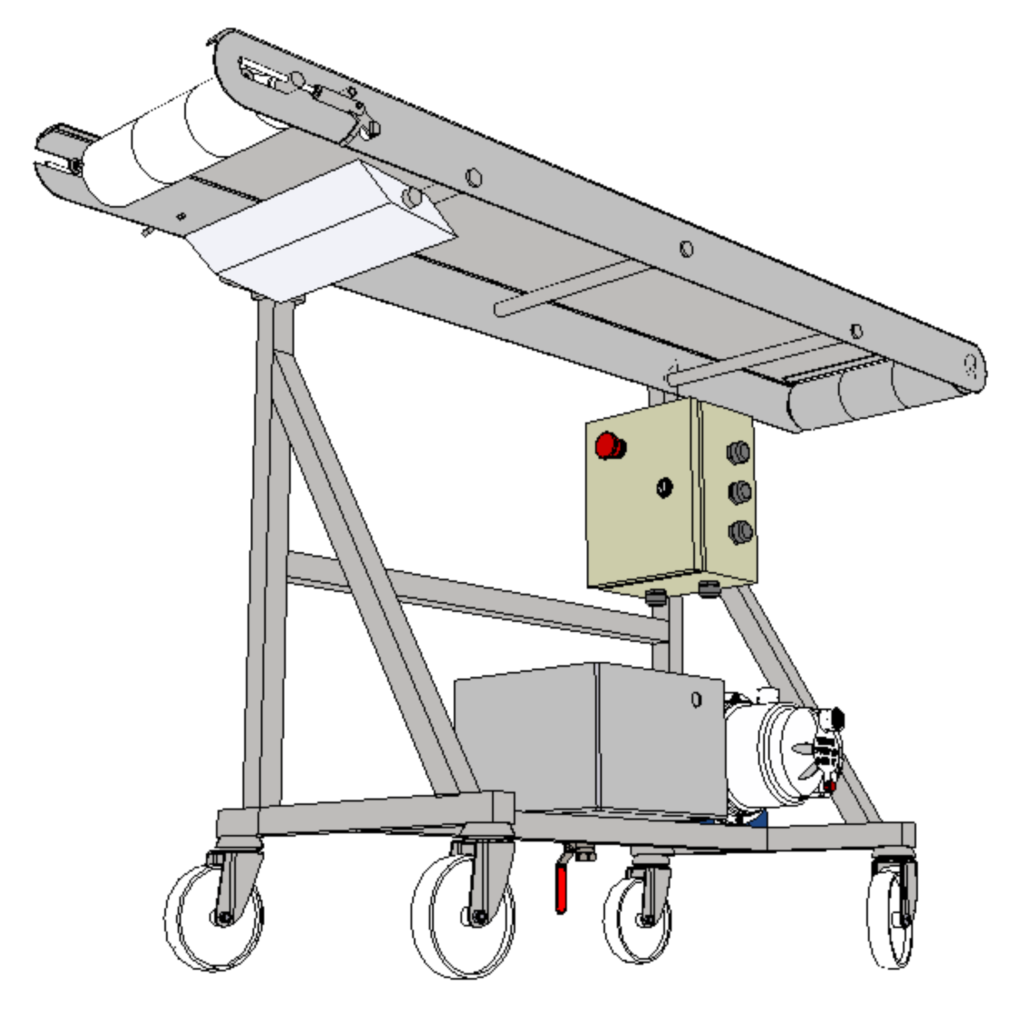
Cry about it.
don’t.
I found myself looking back at my old designs when sorting through an old hard drive. Early on, I made a lot of design mistakes. It was honestly painful to remember some of these.
Anything from:
-using non-standard frame elements, non-standard threads
-fabricating unnecessarily expensive to machine parts
-overly complicated mechanisms
-underperforming mechanisms
-unfeasible ideas
-bugs in PLC code
-using components unsuitable for the job
-using hard to source and expensive devices in the machine
-the good ol’ x-y problem and not knowing how to convince the customer otherwise
The conveyor above:
-Has a quick release toggle tensioner but toggle arm was too thin and prone to breakage.
-Toggle was designed and machined from scratch, waste of time, effort and money.
-The drum motor used was very expensive; 7 years on, it hasn’t failed yet, but I could have done with a lot cheaper.
-There is also an auto oiling spray system, insisted on by the customer. It ended up unused as it caused a lot of extra cleaning and oil wastage. My initial comments to them were “just use a spritz bottle to oil the belt periodically”, which they ended up doing anyway.
The little guy below couples a filler to a former. It’s more of a cobbled together kind of deal, the lofted flange feature also costs too much to fabricate. Ideally I’d have reworked the hopper receiver instead of just cobbling up a hopper-tri-clamp-ferrule thing.
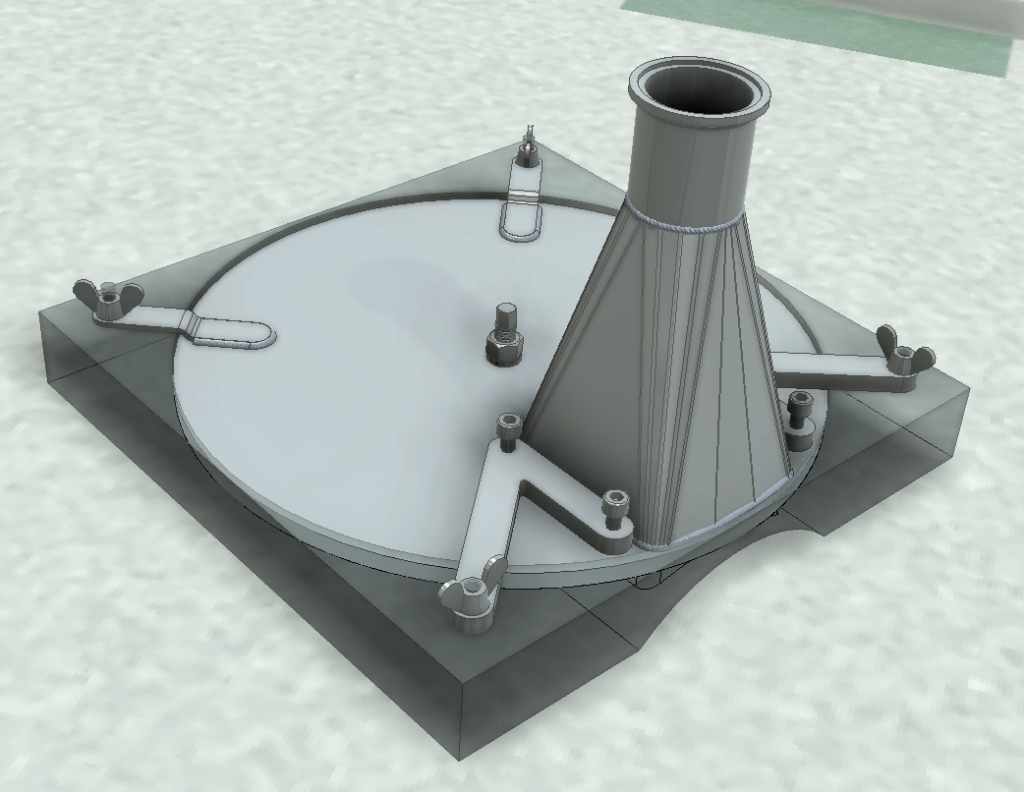
No use crying about it, everyone makes mistakes. Obviously, I still make my fair share of mistakes, but I believe that I’m improving day by day and mistake by mistake. Thankfully, I haven’t had any outright failures so far, most issues were remedied / modified in post.
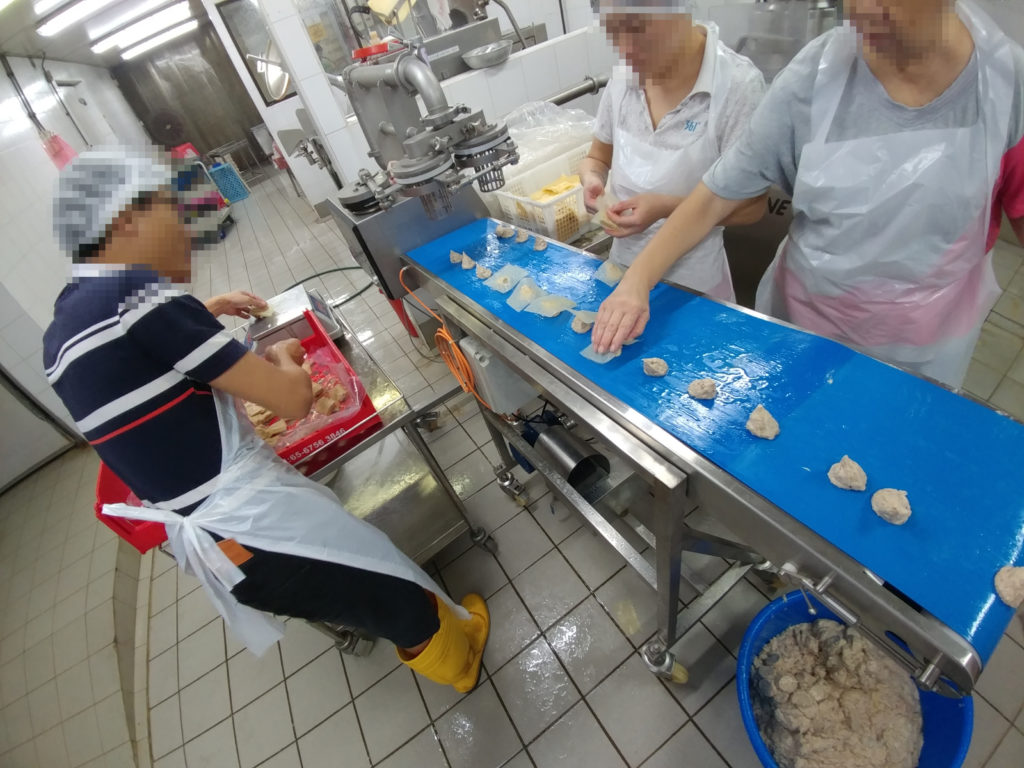
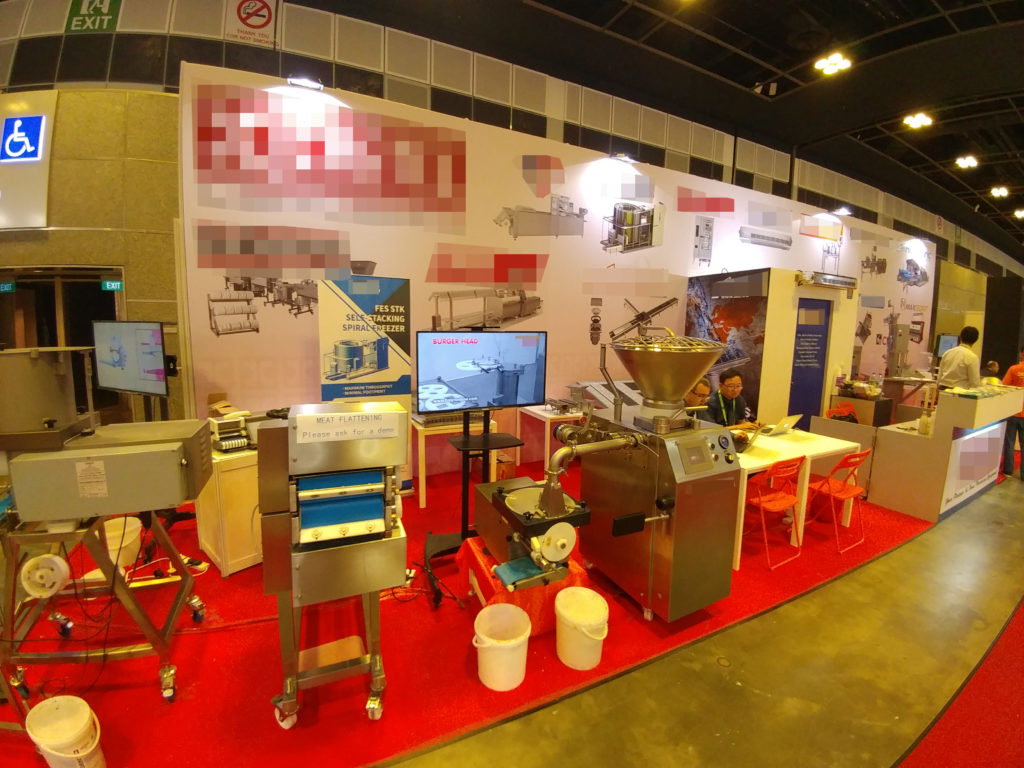
All’s well that ends well~